Chromat #TECHTALKS: 3D Printing
The Chromat Spring/Summer 2015 “Formula 15” Collection included the additive manufacturing technique known as 3D Printing, an exciting Chromat first for the season. With 3D Printed garments now available for purchase at SHOP.CHROMAT.CO, here's a behind-the-scenes look at the in-depth and collaborative process of 3D Printing!
Chromat Curve model Katy Smeyne in the Chromat 3D Printed Facemask
CHROMAT'S GUIDE TO 3D PRINTING (SS15 EDITION)
1. SKETCHES & MODELING
The concept and design phases of 3D Printing began the same way as most Chromat designs do: lots & lots of sketches. To further add further layers of information and detail, the strongest designs were converted into digital illustrations in Adobe Illustrator. We then collaborated with talented architect Juan De Marco, who rendered our 2D sketches into 3D models using Maya.

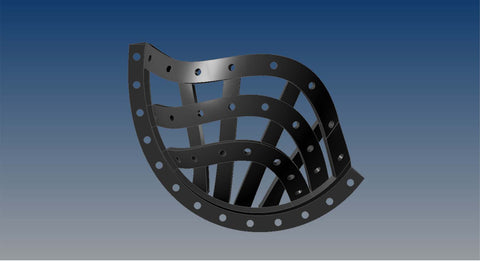
Chromat Bra Cup 3D Renderings by Juan De Marco
The 3D modeling process is more commonly used in architecture and animations fields than in fashion. Chromat continues to draw on our architecture foundations to collaborate with architects and designers outside of fashion to create new, innovative garments.
2. PRINTING
Once the digital models were built, it was time to print! Chromat's 3D printing debut utilized the Makerbot printer with ABS filament (coiled thermoplastic polymer), which melts the plastic filament and releases it in focused bits on the printing surface, building one plane at a time (like layers of a cake, except infinitely more intricate).
Chromat's 3D Printed designs required the Makerbot to print a support structure as well. This support isn't part of the final product, but builds up a raised surface for the bra cup, facemask or skirt pocket to print onto (allowing for the third dimension in the printing process). The printing time for one pair of bra cups is 7 hours; each set of pockets takes up to 19 hours, and each facemask requires 5 hours to print.
3. PRINT DETAILING & FINISH WORK
Close up of the Chromat 3D Printed Skirt
4. GARMENT CONSTRUCTION
Now sanded and smoothed to perfection, Chromat's finished 3D Prints were then integrated into garments using couture hand-sewing techniques by the Chromat production team.
The Chromat 3D Printed Odile Bustier
The 3D Printed end-products mesmerized audiences on the SS15 runway at New York Fashion Week. Utilizing new additive manufacturing techniques has allowed us to develop complex shapes and volumes that would be difficult to achieve using traditional materials and construction methods.
The Chromat 3D Printed Facemask
PRINTED CLOTHING IS THE FUTURE
Chromat is excited for the future in which high-fashion garments are as accessible as music. Until then, 3D printed clothing remains a luxury product that requires a highly-skilled team of modelers, printers, and fashion designers to develop and produce each garment. We look forward to continuing to innovate in the realm of printed clothing for years to come.